
Professional-Grade Welders at a DIY Price
On just about any vehicle restoration or new build project, you'll eventually need to weld metal. Instead of bringing your vehicle to a welding shop or trying to track down a friend with a plasma cutter, shop at Eastwood for automotive welding supplies. We are proud to carry an assortment of shop welders for sale along with the accessories and protective gear that you need for accurate and safe welding.
Who makes Eastwood welders? We do! The R&D team at Eastwood has been developing quality welders and other products for do-it-yourselfers and professionals alike since 1978. Whether you need a small welder for on-the-go repairs, an industrial welder to do large-scale work, or new consumables and safety equipment, we're here to help. Shop online 24/7 for an Eastwood welder or plasma cutter that can help you Do the Job Right.
Eastwood Welding Machines for Every Job
Whatever type of welder is right for your shop, we are here to help you get the best machine at the best price. There are several primary welding processes, each of which has its own equipment requirements.
MIG welders use a metal wire as an electrode and a gas shield. It's the easiest and fast type of welding, making these welders a great beginner option. Generally, the welds aren't as clean looking, so an Eastwood MIG welder is best for underbody work such as exhausts.
TIG welders also have an electric arc but use tungsten for their electrode. TIG welding is harder to learn but produces the best results in terms of quality and appearance.
Stick/Arc welders, also known as torch welders, are the ideal portable welder at a race track or job site. A stick gas welding machine does the best work for undesirable conditions such as dirty surfaces or windy and rainy weather.
Flux-cored welders are a semi-automated version of MIG welders with a flux shield that provides added protection for outdoor welding, making it another good on-the-go option.
Multi-process welders let you easily switch modes depending on the type of weld and the material you're working with. Some welders also include a spool gun that lets the user weld aluminum.
Laser welders offer unparalleled precision, control, and versatility, making them a preferred choice for a wide range of industrial applications where high-quality welds and precise assembly are required. Their ability to weld a variety of materials, their suitability for micro-welding, and their capability for high-volume production make them an indispensable tool in modern manufacturing processes.
Plasma Cutters for Metal Fab
Sometimes you need to cut metal before you can join it together. Eastwood Versa-Cut Plasma Cutters slice through metal cleanly and quickly. They cut more precisely on curves than mechanical cutters and require less elbow grease than handheld metal snips. A 3-in-1 welder and plasma cutter combination will let you slice through metal and then weld it in one continuous process. Eastwood has many welding packages that include a welder, plasma cutter and welding cart at a discounted price.
Trust Eastwood and Never Cut a Corner
Of course, you'll need more than just a welder to complete your next project. Eastwood has all the right products for a successful build. You'll find clamps and tools for holding parts together for welding; surface preparation tools to prepare your welding project; quality consumable wires like filler wire, welding tips and nozzles; and welding carts for rolling equipment around the garage. We also have a full selection of welding helmets welding gloves, respirators and other protective accessories, along with instructional welding books and videos for learning basic or advanced skills.
Complete any welding or metal fabrication project with confidence by choosing Eastwood. Our electric welding units have a three-year manufacturer's warranty so you know we believe in their performance. If you need more information before you buy, visit the How-To Center for buyer's guides, welding tips and other helpful resources. Lifetime tech support is included with each purchase, so call an Eastwood metal fabrication expert today!
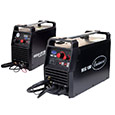


Most Popular in Welding
How to Choose a Welder
What type of welder is best for the project you’re working on? Eastwood breaks it down and asks all the right questions to help you decide which welder is right for you.
Still unsure? Try out our Welder Finder.
Newest in Welding
- Eastwood Versa Cut 4X4 CNC Plasma Table With CNC Cut 40 and Machine TorchReg. $4,436.97 Sale $4,199.97 Save $237.00
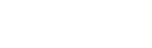
Article: MIG or TIG – Which is Better for Welding Sheet Metal Patch Panels?
Patch panel repairs are one of the most common welding tasks you might encounter when restoring old vehicles. The question often comes up about which method is better for the task – MIG (Metal Inert Gas) or TIG (Tungsten Inert Gas). The short answer is that MIG welding and TIG welding are […]
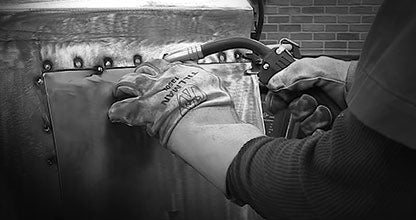
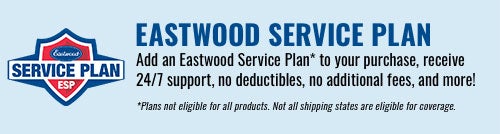
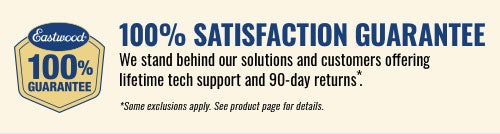
Professional-Grade Welders at a DIY Price
On just about any vehicle restoration or new build project, you'll eventually need to weld metal. Instead of bringing your vehicle to a welding shop or trying to track down a friend with a plasma cutter, shop at Eastwood for automotive welding supplies. We are proud to carry an assortment of shop welders for sale along with the accessories and protective gear that you need for accurate and safe welding.
Who makes Eastwood welders? We do! The R&D team at Eastwood has been developing quality welders and other products for do-it-yourselfers and professionals alike since 1978. Whether you need a small welder for on-the-go repairs, an industrial welder to do large-scale work, or new consumables and safety equipment, we're here to help. Shop online 24/7 for an Eastwood welder or plasma cutter that can help you Do the Job Right.
Eastwood Welding Machines for Every Job
Whatever type of welder is right for your shop, we are here to help you get the best machine at the best price. There are several primary welding processes, each of which has its own equipment requirements.
MIG welders use a metal wire as an electrode and a gas shield. It's the easiest and fast type of welding, making these welders a great beginner option. Generally, the welds aren't as clean looking, so an Eastwood MIG welder is best for underbody work such as exhausts.
TIG welders also have an electric arc but use tungsten for their electrode. TIG welding is harder to learn but produces the best results in terms of quality and appearance.
Stick/Arc welders, also known as torch welders, are the ideal portable welder at a race track or job site. A stick gas welding machine does the best work for undesirable conditions such as dirty surfaces or windy and rainy weather.
Flux-cored welders are a semi-automated version of MIG welders with a flux shield that provides added protection for outdoor welding, making it another good on-the-go option.
Multi-process welders let you easily switch modes depending on the type of weld and the material you're working with. Some welders also include a spool gun that lets the user weld aluminum.
Laser welders offer unparalleled precision, control, and versatility, making them a preferred choice for a wide range of industrial applications where high-quality welds and precise assembly are required. Their ability to weld a variety of materials, their suitability for micro-welding, and their capability for high-volume production make them an indispensable tool in modern manufacturing processes.
Plasma Cutters for Metal Fab
Sometimes you need to cut metal before you can join it together. Eastwood Versa-Cut Plasma Cutters slice through metal cleanly and quickly. They cut more precisely on curves than mechanical cutters and require less elbow grease than handheld metal snips. A 3-in-1 welder and plasma cutter combination will let you slice through metal and then weld it in one continuous process. Eastwood has many welding packages that include a welder, plasma cutter and welding cart at a discounted price.
Trust Eastwood and Never Cut a Corner
Of course, you'll need more than just a welder to complete your next project. Eastwood has all the right products for a successful build. You'll find clamps and tools for holding parts together for welding; surface preparation tools to prepare your welding project; quality consumable wires like filler wire, welding tips and nozzles; and welding carts for rolling equipment around the garage. We also have a full selection of welding helmets welding gloves, respirators and other protective accessories, along with instructional welding books and videos for learning basic or advanced skills.
Complete any welding or metal fabrication project with confidence by choosing Eastwood. Our electric welding units have a three-year manufacturer's warranty so you know we believe in their performance. If you need more information before you buy, visit the How-To Center for buyer's guides, welding tips and other helpful resources. Lifetime tech support is included with each purchase, so call an Eastwood metal fabrication expert today!